What Is Calibration in Batching Equipment?
Calibration refers to the process of verifying and adjusting the measuring instruments and controls of batching equipment to ensure they operate within specified tolerances. This includes weighing systems, moisture sensors, temperature gauges, and automated control units.
Batching equipment must consistently deliver the correct quantities of materials — aggregates, cement, water, and additives — to maintain mix design specifications. Calibration guarantees that your equipment measures and dispenses materials accurately, avoiding costly errors.
Why Is Routine Calibration Essential?
1. Ensures Consistent Product Quality
Concrete and asphalt quality rely on precise proportions of ingredients. Even slight deviations in material quantities can lead to weaker concrete strength or asphalt that doesn’t meet durability standards. Regular calibration keeps batching equipment delivering exact volumes, resulting in a consistent and high-quality final product.
2. Reduces Material Waste and Costs
Overdosing materials due to inaccurate weighing or measuring increases production costs and wastes valuable resources. Calibration minimizes these errors, helping plants reduce material wastage and save money over time.
3. Maintains Regulatory Compliance
Many countries have stringent construction and environmental regulations requiring producers to adhere to specific mix designs and environmental standards. Calibration ensures that your plant complies with these laws, avoiding fines or shutdowns.
4. Improves Operational Efficiency
Accurate equipment reduces the frequency of batch rejects and reworks, speeding up production cycles. This leads to higher throughput, better resource utilization, and increased profitability.
5. Prolongs Equipment Lifespan
When equipment operates outside its specified parameters, it faces increased wear and tear. Routine calibration helps detect mechanical issues early, preventing breakdowns and extending the life of costly batching machinery.
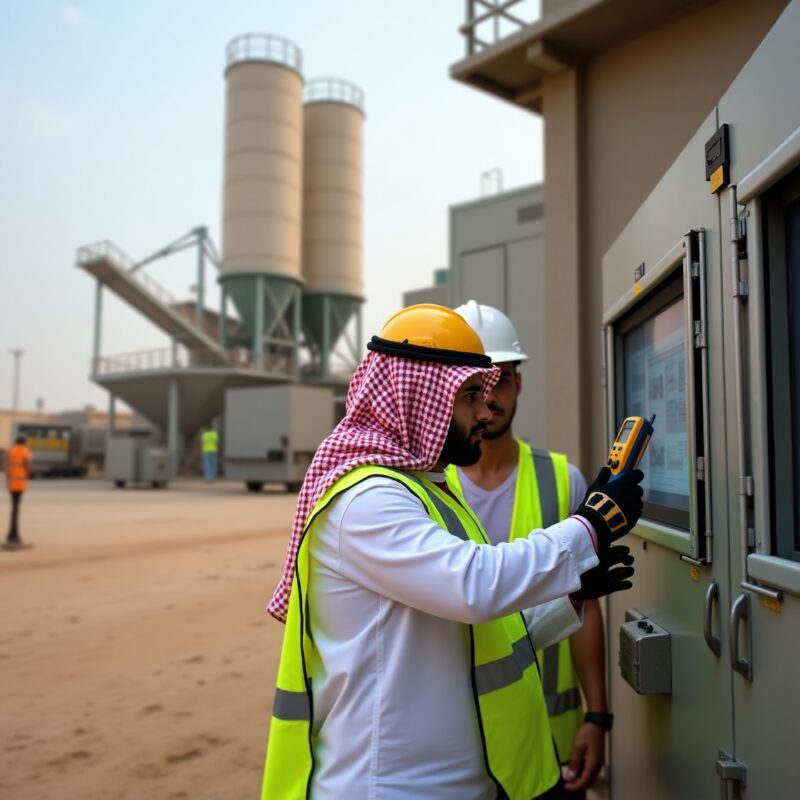
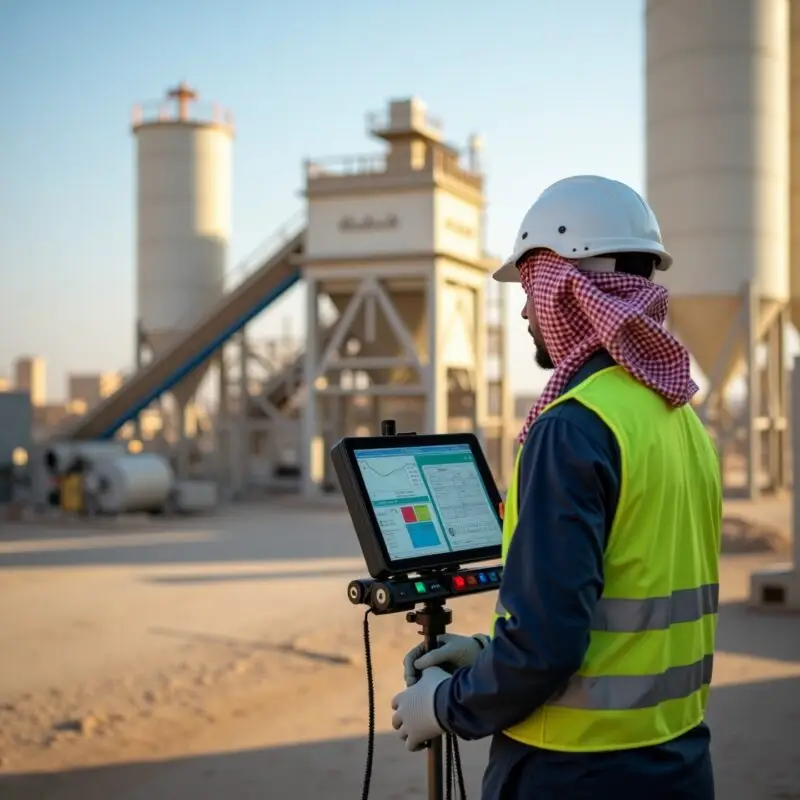
Which Equipment Requires Routine Calibration?
Routine calibration should be performed on all critical batching components, including:
- Weighing scales for aggregates, cement, and additives
- Water flow meters and moisture sensors
- Temperature sensors in drying or mixing units
- Control panels and automation systems
- Conveyor belt speed controls
The Role of Spare Parts in Maintaining Calibration
Calibration efforts can be undermined by worn or substandard parts. Using genuine, high-quality spare parts is crucial to maintaining equipment accuracy. Common parts affecting calibration include load cells, sensors, valves, and control boards.
A well-managed spare parts inventory enables quick replacements, minimizing downtime and ensuring your plant consistently meets calibration standards.
Conclusion
Routine calibration of batching equipment is more than a regulatory requirement—it’s a fundamental practice that safeguards product quality, reduces waste, and boosts operational efficiency. Neglecting calibration can lead to costly errors, increased downtime, and regulatory risks.
By prioritizing calibration and using high-quality spare parts, asphalt, concrete, and crusher plants can maintain peak performance, ensure customer satisfaction, and stay competitive in the market.
A well-managed spare parts inventory enables quick replacements, minimizing downtime and ensuring your plant consistently meets calibration standards.