What Is Calibration in Batching Equipment?
Calibration refers to the process of verifying and adjusting the measuring instruments and controls of batching equipment to ensure they operate within specified tolerances. This includes weighing systems, moisture sensors, temperature gauges, and automated control units.
Batching equipment must consistently deliver the correct quantities of materials — aggregates, cement, water, and additives — to maintain mix design specifications. Calibration guarantees that your equipment measures and dispenses materials accurately, avoiding costly errors.
Understanding Bitumen and Why Line Blockages Occur
Bitumen is naturally thick and requires heating to flow efficiently through pipelines. In most asphalt plants, bitumen is kept at temperatures between 140°C and 180°C to maintain optimal viscosity.
If bitumen cools too much while inside the pipeline or faces temperature inconsistencies, it thickens and can solidify, leading to clogs or blockages. These blockages are not only disruptive but can also cause equipment damage and increase maintenance costs.
Common causes of bitumen line blockages:
- Uneven or insufficient heating along pipelines
- Poor or damaged insulation on bitumen lines
- Improper shutdown procedures that leave bitumen inside the pipes to cool
- Design flaws, such as low spots or inadequate slope that trap bitumen
- Air leaks or oxidation, which alter bitumen’s chemical properties
How Hot Climates Affect Bitumen Line Management
Operating in hot environments like the Middle East or other tropical regions introduces additional challenges:
- Overheating external surfaces can degrade bitumen inside the pipeline, causing hard residues or “coking.”
- Temperature fluctuations between day and night create expansion and contraction stresses, affecting pipe integrity.
- Heat can affect temperature sensors and insulation effectiveness, leading to inaccurate temperature control and uneven heating.
Hence, effective temperature management and system design become even more critical in hot climates to prevent line blockages.
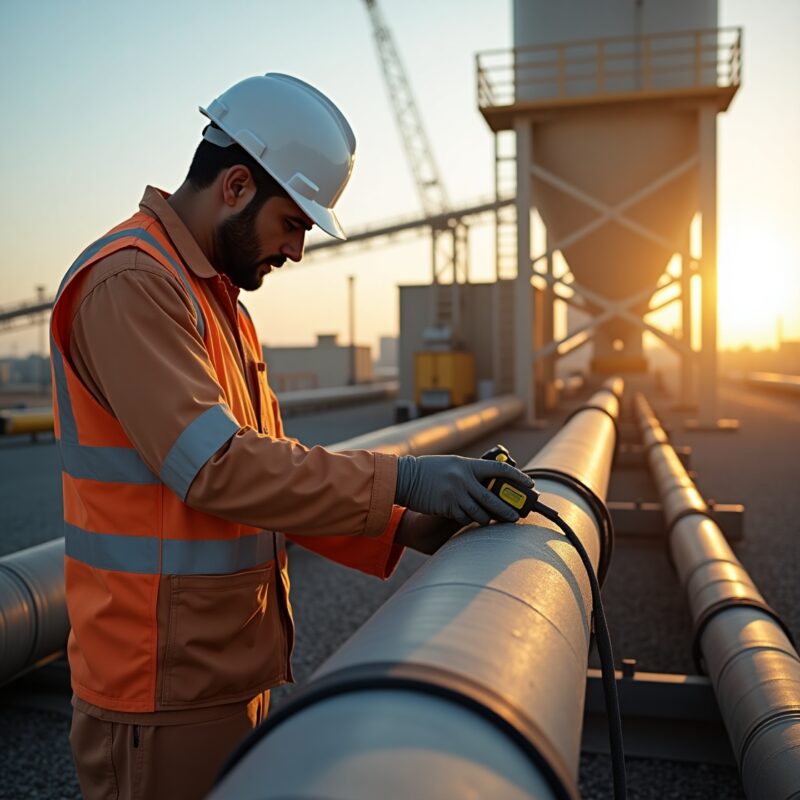
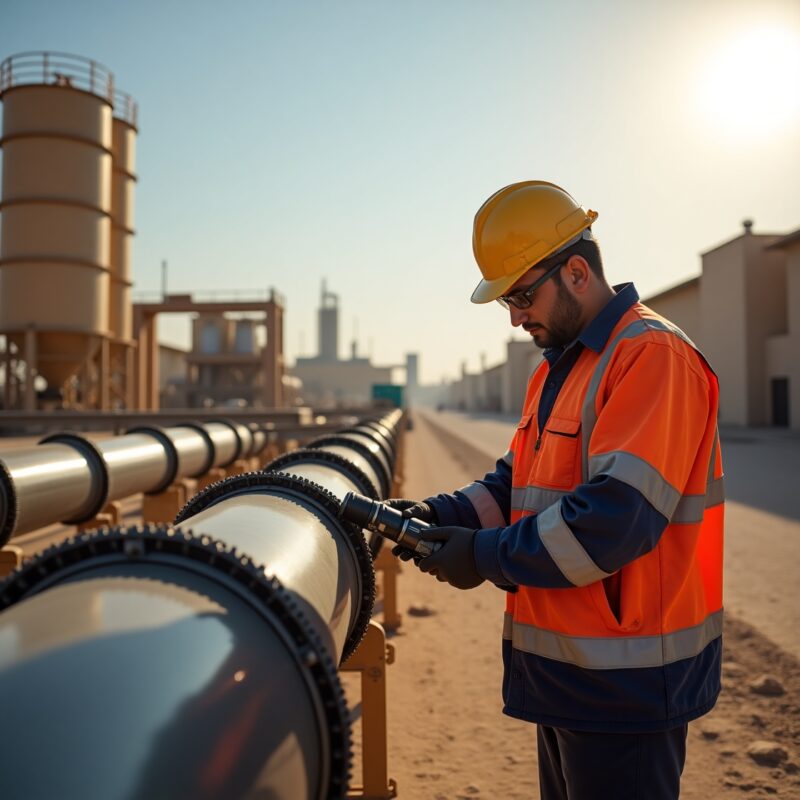
Effective Strategies to Prevent Bitumen Line Blockages
1. Install High-Quality Thermal Insulation
Ensure that all bitumen lines, valves, and fittings are covered with durable, heat-resistant insulation. This helps maintain consistent temperatures by preventing heat loss and protecting against external temperature extremes.
2. Use Continuous Heat Tracing Systems
Electric heat tracing cables or oil-jacketed heating systems keep bitumen at the right temperature throughout the pipeline. Implement zoned temperature control to regulate heat precisely, avoiding both overheating and underheating.
3. Develop Strict Shutdown and Drain Procedures
Always drain bitumen lines before shutting down equipment for extended periods. If complete drainage isn’t possible, use automatic drainage valves to prevent solidification inside the pipes.
4. Regular Flushing and Cleaning
Schedule routine flushing with hot oil or compatible solvents to clear out any buildup or residues inside pipelines. This prevents partial blockages from developing into full clogs.
5. Monitor Temperature Continuously
Use temperature sensors at critical points along the pipeline and connect them to an alarm system that notifies operators if temperatures fall outside preset limits. This real-time monitoring allows prompt action.
6. Optimize Pipeline Design
Ensure pipelines are designed with a slight slope toward the receiving tanks to facilitate natural flow and drainage. Avoid sharp bends and low spots that could trap bitumen and cause stagnation.
7. Maintain a Spare Parts Inventory
Stock essential parts like valves, gaskets, heating cables, and sensors to enable quick repairs or replacements. This reduces downtime in case of component failures.
Conclusion
Preventing bitumen line blockages in hot climates demands a combination of proper heating, pipeline insulation, good design, and regular maintenance. With the right systems in place, asphalt plants can enjoy smoother operations, reduce costly downtime, and extend equipment life.
By implementing these strategies and maintaining a reliable supply of spare parts, plant operators can confidently handle the unique challenges posed by hot environments — ensuring efficient bitumen transport and consistent asphalt quality.
By prioritizing calibration and using high-quality spare parts, asphalt, concrete, and crusher plants can maintain peak performance, ensure customer satisfaction, and stay competitive in the market.
A well-managed spare parts inventory enables quick replacements, minimizing downtime and ensuring your plant consistently meets calibration standards.