What is Burner Calibration?
Burner calibration refers to the process of adjusting a burner to ensure it delivers the correct air-fuel mixture for optimal combustion. This includes setting proper fuel flow, air ratio, ignition timing, and flame characteristics. Poorly calibrated burners can lead to production delays, inconsistent concrete mix quality, and excessive fuel consumption.
Accurate calibration ensures that burners operate within their designed parameters, delivering reliable heating without wasting fuel or creating unsafe conditions. It also helps balance pressure levels, monitor flame shape, and prevent buildup of carbon deposits within the combustion chamber.
Batching equipment must consistently deliver the correct quantities of materials — aggregates, cement, water, and additives — to maintain mix design specifications. Calibration guarantees that your equipment measures and dispenses materials accurately, avoiding costly errors.
Why Burner Calibration Matters in Concrete Plants
- Fuel Efficiency and Cost Savings
A well-calibrated burner consumes less fuel by achieving maximum combustion efficiency. This means lower operational costs and reduced carbon emissions. Faulty or degraded components often result in overuse of fuel or incomplete combustion, increasing expenses and impacting performance.
- Consistent Heating for Concrete Quality
Inconsistent heating of aggregates can lead to variations in concrete mix quality. Burner calibration ensures even and reliable heat distribution, supporting more uniform batching and higher-quality end products.
- Environmental Compliance
Modern concrete production facilities must meet strict emissions standards. A correctly calibrated burner emits fewer pollutants, helping plants stay compliant with environmental regulations while reducing their carbon footprint.
- Longer Equipment Life
Excessive heat, soot buildup, and fluctuating pressure caused by an uncalibrated burner can reduce the lifespan of concrete plant components. Regular calibration, supported by dependable spare parts, helps protect your investment and extends equipment longevity.
- Enhanced Safety and Stability
Burner instability — such as flameouts, pressure spikes, or erratic ignition — can be dangerous. Calibration ensures safe operation by preventing such issues, creating a safer environment for workers and reducing the risk of costly repairs.
Bitumen is naturally thick and requires heating to flow efficiently through pipelines. In most asphalt plants, bitumen is kept at temperatures between 140°C and 180°C to maintain optimal viscosity.
If bitumen cools too much while inside the pipeline or faces temperature inconsistencies, it thickens and can solidify, leading to clogs or blockages. These blockages are not only disruptive but can also cause equipment damage and increase maintenance costs.
Warning Signs Your Burner Needs Calibration
If your burner system is experiencing any of the following issues, it may be time to schedule a calibration:
- Fluctuating or inconsistent temperatures
- Abnormal smoke or odor from the burner stack
- Increasing fuel bills without increased production
- Irregular flame behavior (color, shape, or intensity)
- Unexplained shutdowns or ignition failures
These symptoms often indicate the need for new parts or a complete recalibration of your burner unit.
Role of Spare Parts in Effective Burner Calibration
High-quality spare parts are the foundation of precise burner calibration. Over time, components wear out, become corroded, or lose sensitivity, leading to poor performance and inefficient combustion. Replacing them during calibration helps restore your burner’s original performance levels.
Key Spare Parts That Support Calibration:
- Ignition electrodes and flame detectors: These are essential for safe ignition and real-time flame monitoring.
- Burner nozzles and heads: Ensure correct fuel atomization and stable flame shape.
- Fuel control valves and solenoids: Regulate fuel flow for precise combustion.
- Air pressure regulators: Maintain correct airflow for optimal air-fuel mix.
- Air pressure regulators: Maintain correct airflow for optimal air-fuel mix.
By using genuine or OEM-quality parts, concrete plant operators can ensure compatibility, performance, and safety.
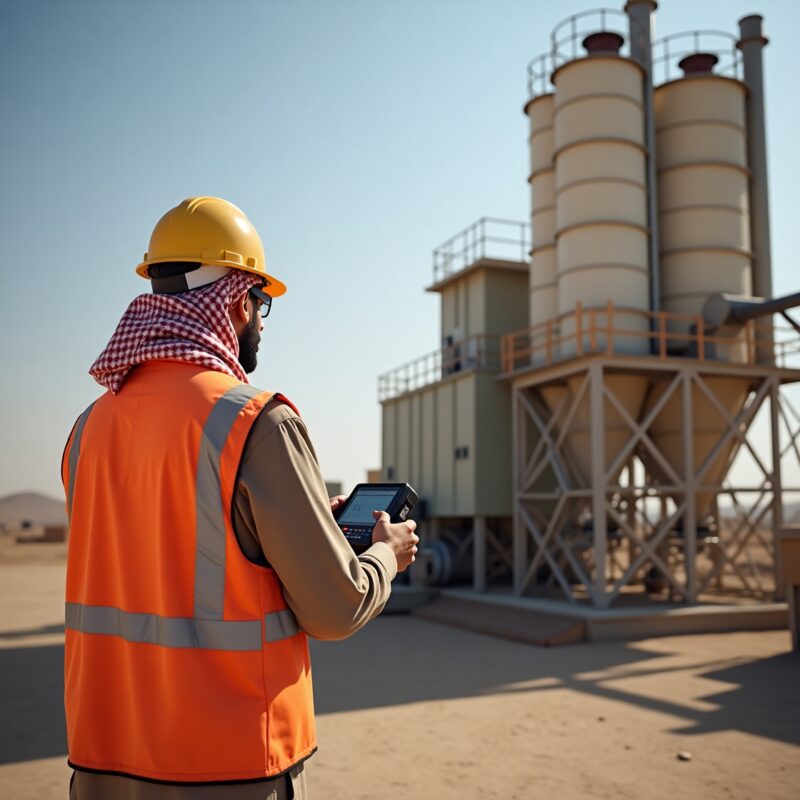
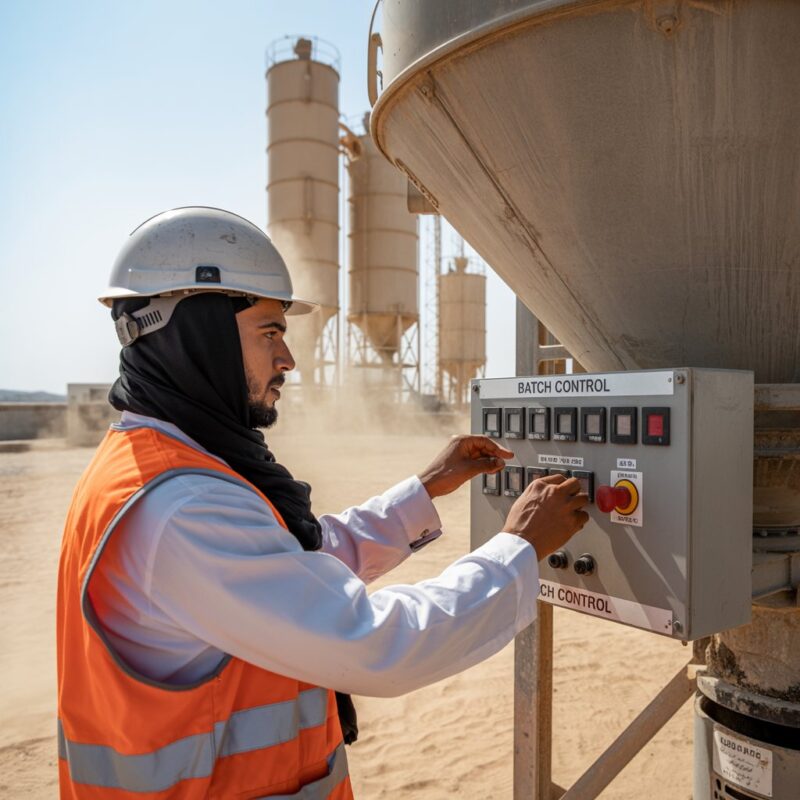
A Strategic Approach to Concrete Plant Uptime
Burner calibration shouldn’t be an afterthought. It’s a vital aspect of plant efficiency and safety that directly impacts the bottom line. Well-maintained burner systems lead to stable production cycles, lower operational costs, and better-quality concrete output.
With the right parts and proactive maintenance, your burner system can deliver consistent performance year-round — even under tough environmental or production conditions.
Road Engineering Trading Establishment supports this critical need by supplying a wide range of dependable electrical and mechanical parts tailored for concrete plant burner systems. With the right parts in stock, plant operators can ensure reliable, efficient, and safe operations every day.
With the right parts and proactive maintenance, your burner system can deliver consistent performance year-round — even under tough environmental or production conditions.